Waterjet cutting machines are precision tools for a wide range of applications. Thanks to a special feature, waterjet cutting has a great advantage over other cutting processes. A used waterjet cutting machine is a favorable alternative for many companies.
Waterjet cutting by waterjet cutting machine briefly explained
Water jet cutting is a manufacturing process in which a specific workpiece is cut with a water jet. In contrast to shredding or chipping, the individual layers of the processed material are not separated mechanically, but are removed. Cutting and separating with a water jet is a cold separation process and at least as precise as laser cutting. Water Jet and Microwaterjet, for example, cuts all materials reliably and safely.
The machine has a special cutting system that allows water to act on the material surface at a high pressure of up to 6000 bar and an outlet speed of up to 1000m/s. The resulting material removal consists exclusively of near-surface and microscopically small particles. Friction can thus not occur to any significant extent. This is the big difference to other ablation methods (laser, oxy-fuel and plasma methods), which are all based on thermal energy.
Different variants and different materials
The wide range of possible applications shows just how important it is to pay attention to quality even with second-hand machines. On the one hand, waterjet cutting has different effects and effects depending on the material properties. In the case of workpieces made of brittle and harder materials (such as cast iron or ceramics), the material is removed by the microcracks in the surface caused by the water pressure, which spread, unite and ultimately remove the particles. Tough materials such as steel initially deform plastically or irreversibly when processed with a waterjet, resulting in so-called work hardening. This microscopically small change results in embrittlement of the material, which makes removal possible. An inexpensive waterjet cutter can process almost all materials. The spectrum ranges from soft foam to the hardest gemstones (such as sapphire). On the other hand, a distinction is made between two methods. In waterjet cutting with pure water, the soft materials (foams, paper, foils, certain plastics, etc.) are separated from each other. For abrasive cutting, a hard and powdery abrasive (“abrasive”) is added to the water in order to be able to remove the particularly hard materials such as ceramics, steel or certain precious stones.
What can water jet cutting be used for?
This is about manufacturing with the highest precision. For example, special precision and micro water cutters are able to cut even the smallest medical implants with their water jet, thanks to the microscopically small ablations. Thanks to the temperature-neutral processing, there is no deformation. A waterjet can also be used in combination with other machine tools. A future scenario would be, for example, the finishing of a model produced by a 3D printer. The possibilities for using a waterjet cutter are as versatile as the application itself.
What are the business benefits of used cutting systems or waterjet cutting machines?
Because waterjet cutting does not apply heat or machining forces to the material, the cuts can be made without stretching the workpiece. For such purposes, good and inexpensive second-hand waterjet cutting machines are ideal. Used cutting systems offer not only financial incentives. A waterjet cutting machine offers the best conditions for companies that have to cut a wide variety of materials with millimeter precision in production engineering.
What should be considered when purchasing inexpensive waterjet cutters?
Used machines do not only make sense if the budget for an acquisition is limited. Provided that they are of adequate quality, second-hand machine tools are an affordable alternative. There are enough offers and used machine service. Machines of well-known manufacturers are not only available on the Internet to buy used machines. A good cutting machine does not have to be unaffordable. Spare parts can also be purchased second-hand, whereby a new purchase should be considered from case to case. It is worthwhile not to pay attention to the price in the first place with the wearing parts. But also other machines like CNC milling machines or similar machines are often bought used. A well-maintained used plant is very stable in value.
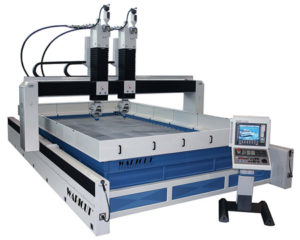
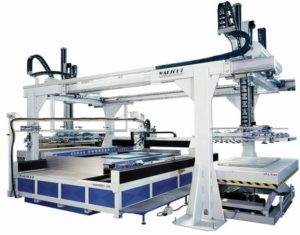
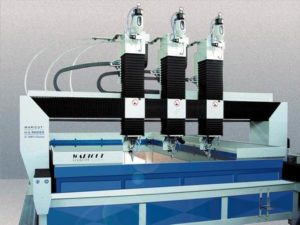